One of Australia's largest national engineering firms contacted us, wanting a solution to the time-consuming and costly refurbishment of heat exchangers used in alumina production.
Usually, the time and cost taken to refurbish these units are significant and expensive, especially when it comes to cleaning, machining, and preparing tube sheets and baffle plates.
The refurbishment's cleaning, machining, and preparation phase generally lasts 60 hours and requires 10 machine operators.
However, a new procedure implemented with the Alpha VersaDrive range, featuring modular, quick change cutting and drilling tool accessories, resulted in a sizeable 300-hour reduction per unit in both time and manpower.
There are several other safety benefits when using these new high-performing products, including a massive reduction in noise usually produced by traditional techniques and potential injury caused by vibration.
Tube sheets (1000 holes)
The reaming of tube sheets at this Australian engineering firm initially took 2 days (4 shifts), equalling 48 hours. Due to breakage, this process consumed at least 3 reamers.
The Alpha VersaDrive range has now reduced their process to half a day, which is less than 1 shift (6 hours) —that's a mammoth saving of 42 hours!
In total, 1 reamer completed 4000 holes (4 tube sheets). With each reamer costing $1000, this company could save $5000 (5 reamers).
Baffle plates (internal)
(Steel LP 3000 holes and Duplex HP 4000 holes)
The costly and time-consuming procedure for baffle plates initially took 10 days (20 shifts), equalling 240 hours. This process ate through 40 carbide burrs ($67 each) and 2 die grinders ($100 each).
The Alpha VersaDrive range slashes the lengthy process down to just 3 days (6 shifts), equalling 72 hours compared to a whopping 240. Plus, the new procedure only consumes 2 No3 reamers per entire heater —that's 2000 holes per reamer.
In total, that's $880 saved and a monumental 168 hours of hard labour diverted. This does not include significant dollar amounts saved due to Personal Protective Equipment (PPE), which is now no longer needed for this operation.
Click on the image below to see the complete range of VersaDrive products
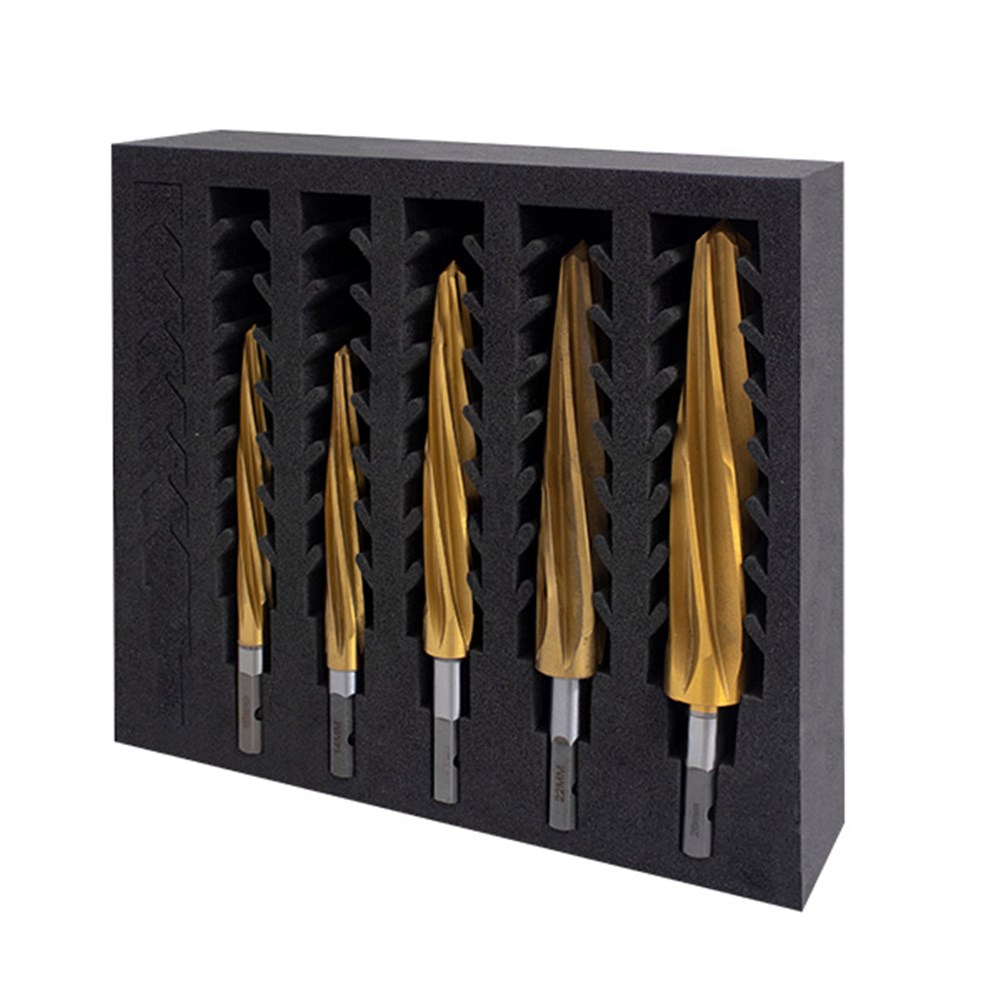
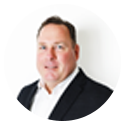
About the Author
Karl Stutterheim